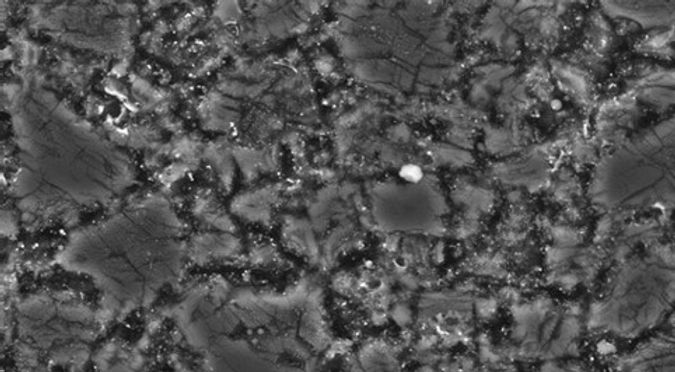
TOWARDS STABLE CRYSTAL NETWORK
JUNE 2022
While todays PDC cutters resist 30 times more compared to what it was 10 years ago, SCT new sample pushed the borders further.
​
Achieving this goal is a tall order, but there will be more rooms for improving cutter performance by controlling manufacturing process parameters and adequate material selection.
​
The boding in between diamond poly-crystal structure is made using a metal catalyst, which is generally cobalt. Due to the different coefficients of expansion, it expands more than diamond when heated up during drilling and causes cracks to develop and leading to cutter failure. Meanwhile in presence of cobalt in polycrystalline diamond compact structure, diamond tends to change to graphite when heated up and causes widespread graphitization. Although making catalyst-free PDC is possible but itwich is d is not commercially viable as it requires ultra high pressure-ultra high temperature (UHPHT) technology with the pressure range of 14 GPa which is twice HPHT requirement.
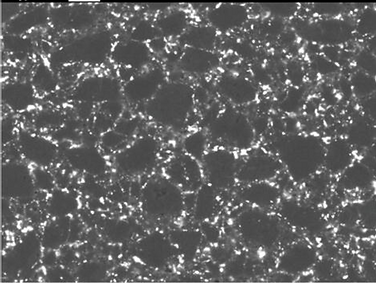
PDC MICROSTRUCTURE WITH COBALT
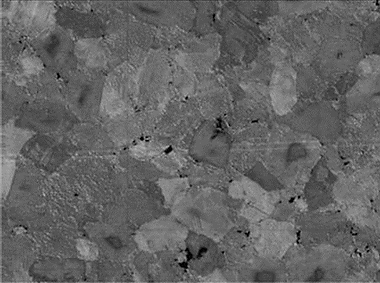
CATALYST-FREE PDC MICRO STRUCTURE
The main goal was enabling PDC cutter stand longer against high temperature generated while drilling hard formations. With metallic ingredient inside diamond structure, PDC damages above 750°C. This limit can been pushed away up to 1200°C utilizing a process caused the metallic catalyst dissolved using acid leaching.

UNLEACHED PDC MICROSTRUCTURE CRACKING AT ELEVATED TEMP
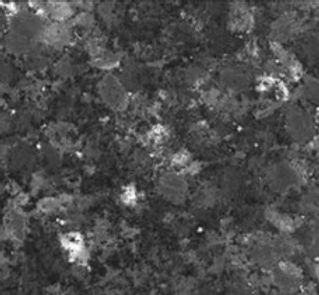
EACHED PDC MICROSTRUCTURE CRACKING AT ELEVATED TEMP

DIAMOND GRAPHITIZATION OF PDC MICROSTRUCTURE WITH METALLIC CATALYST AT HIGH TEMP.
While SCT is working to improved leaching methods , in order to find an affordable way to push those limits higher, we focused on re-engineering of the molecular structure of the PDC. In a series of attempts by SCT’s team, effect of utilizing different metallic catalysts such as Iron, Nickel, Cobalt, Tungsten and their alloys as well as nanomaterials was surveyed.
​
The nanotechnology was practiced and nanoparticles pushed the metallic grains away by filling the internal space around the diamond particles after polycrystalline bonding created.
​
SCT’s new findings are planned to be re-tested in industrial scale and evaluated for cost-effectiveness when the production line is set-up in Canada as its final destination.